By Alex Willis, Senior Manager, Industry and Public Affairs
Technology continues to advance the auto industry at a rapid clip, fueling the race towards enhanced driver and passenger experiences and providing efficiencies in the vehicle purchase journey through digital tools, while easing loads on workers in vehicle manufacturing facilities. These technologies (and much more) were on full display in this year’s Consumer Electronics Show (CES), which has become an important showcase for the industry. Automated driving, electrification, and connectivity were all featured heavily – signs that riders and drivers will have safer vehicles, more vehicle options, and better transportation experiences. It can be daunting to try to take in all the trends, even when focusing on only one industry! There is, however, a common and important lens through which to view these developments and understand them: the human element.
For every delivery bot or large language model, there is a team of engineers constantly working with the technology to make it just right. Oftentimes, even the most advanced robots have a handler or someone monitoring it. So, with all the excitement (and, at times, fear) that might accompany burgeoning technologies, there is one aspect that has remained constant: people. At the center of it all are users, workers, researchers, and many others who take great ideas and make them a reality.
This is something the auto industry has taken to heart for decades, which can take many forms all along the automotive value chain.
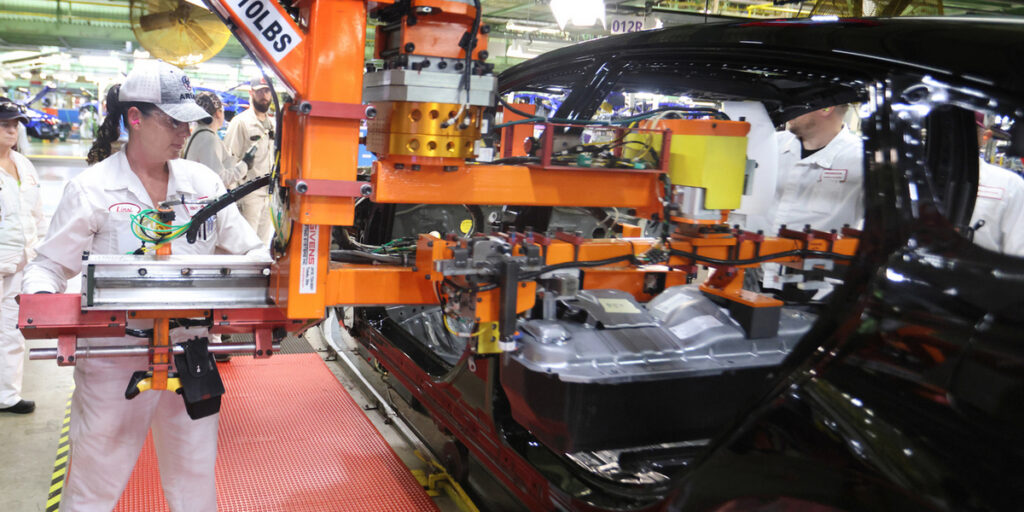
For instance, Honda engages their workforce through a program called “Associate Voice,” where workers at every level of the company can provide input on anything from broader company policy to the manufacturing process. The human element is also especially impactful at the dealer level, where there are touchpoints to discuss in-vehicle technologies with consumers and where technicians ensure the safety and reliability of these “computers on wheels.” Stories from individuals like Nelly Colón, who has worked to break down barriers and is succeeding as one of a small group of Master Technicians at Nissan dealerships across the country, are important reminders of how critical a personal touch can be to enhancing user experience and improving people’s lives.
As manufacturing has become more advanced, automakers have automated many of the most challenging jobs on the assembly line, but they haven’t removed humans from the process. In many cases, a person and machine co-work on the vehicles. Some even give workers harnesses or mechanically assisted tools to use to reduce repetitive stress injuries. What’s more, the lessons learned from manufacturing can sometimes translate to other areas like assistive robotics, where Toyota is making strides.
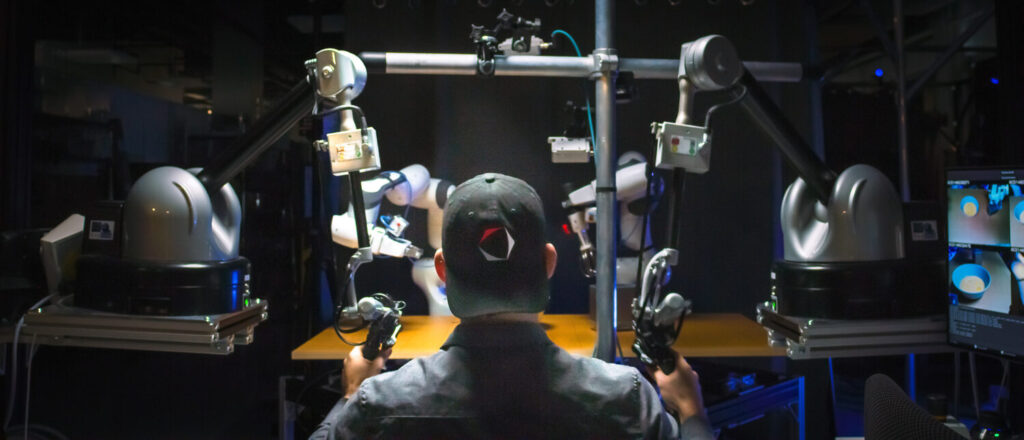
Without a doubt, it is important to look at the future and understand how the very nature of the auto industry is changing. Taking a moment to appreciate that each of the millions of vehicles and engines JAMA members produced in the U.S. were manufactured and engineered by at least one, if not hundreds, of hardworking Americans employed at Japanese-brand automakers’ facilities, is powerful. It shows that even as technology advances, and things become increasingly complex, it’s still the people that make it all work.